Most of us use products every day without putting too much thought into how those products were made. For example, the keyboard I’m using to write this piece has printed letters on each key, but how did these keys get printed with letters exactly? The answer is that they were pad printed with the letters. Let’s get into what pad printing is and how it’s used in several different industries.
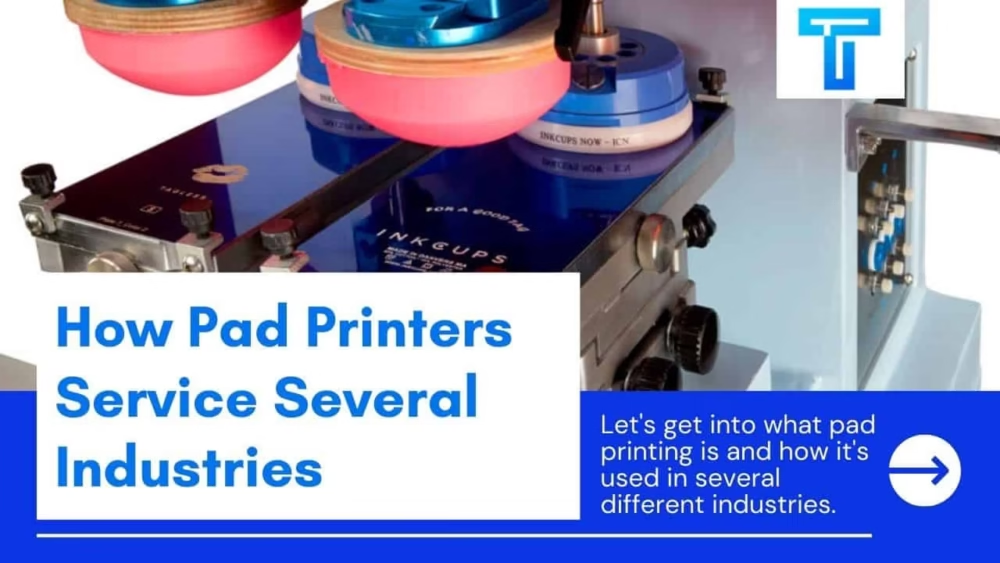
What is Pad Printing?
The name gives a bit of a clue into how the process of how pad printers work. Pad printers work by transferring ink from a silicone pad into the product you want to print on. A simple way to think about this is the stamps you probably used when making crafts as a child. The pad printers typically hold the product while the pad stamps the product with the desired print. Once the item is printed, the product is left to air dry for the ink to harden.
Pad printing equipment is used in today’s commercial applications in order to print a lot of products in a short amount of time. This means that this printing technique is often used on mass-produced products and is found on many assembly lines within large factories.
The Pros To Pad Printing
The biggest pro to pad printing is the versatility of this type of printing method and equipment. This type of printing can be used on almost anything, which gives factories and manufacturers a lot of freedom. This also means that pad printing equipment can be modified and adjusted in order to print on different products, giving these sorts of machines a long shelf life.
Another big pro to pad printing aside from its versatility is that it’s a great way to print 3d surfaces, as well as products of any shape and size. This means that your item can be curved or have uneven surfaces and pad printing will still be able to put a high-quality print on the product. As mentioned earlier, keyboard keys are a great example of this as they are concaved in shape to be comfortable to the fingers, but a pad printer can put a high-quality stamped letter on each key regardless of the key shape.
Another huge pro of pad printing is that of consistency. Because a robot can be the applicator, the same pressure and ink amounts can be consistent across a wide array of stamped products. This is a huge plus for products made at a scale that require consistent prints.
Custom Solutions
Each factory is different, and the production equipment is customized in order to create products of all shapes and sizes. Because of this, pad printing also needs to be integrated into your manufacturing process in order to work seamlessly in production. Thankfully there are solutions out there where pad printing solutions can be crafted for simple operations as well as very complex manufacturing processes. These solutions typically involve pad printing by a robot, tray, vibratory bowl, or operator. A pad printing engineer can help you to decide what medium will work best in order to save you time, money, and increase the efficiency of your production process when it comes to printing.
With most of the manufacturing moving to completely automated processes, having a good pad printing engineering firm is pivotal in order to help you reduce the manpower needed in order to get your products printed. Elements of pad printing automation include feeding, fixture, pre-inspection, treatment, printers, post-cure, vision inspection, and unloading. All of these elements should be addressed by a pad printing engineer in order to help you get the most out of pad printing automation.
Industries That Use Pad Printing
One of the largest industries that utilize pad printing is that of the automotive industry. Just think about all of the buttons, dials, and other dashboard items that have something printed on them to help users understand what they do. All of these prints are typically made using pad printing techniques.
Sporting equipment is another large industry that utilizes this printing method due to the rigid and curved shapes that most sporting equipment entails. The next time you put on a baseball helmet and see the printing on it, you’ll know how it was done!
Medical devices also utilize pad printing as they come in all shapes and sizes. Pad printing can make labeling buttons and instructions for use on these types of products a much easier process than that of other printing methods. Since medical devices are made on a large scale, pad printing has become one of the most cost-effective ways to get these sorts of products labeled with ink.
One common misnomer is that pad printing can only support products that need printing done in one color. This is not true as pad printing can be used with multiple colors and can be transferred sequentially to the product. This opens up quite a bit of flexibility and allows many different types of products to be able to be pad printed.
As you can see, pad printing is used in multiple industries due to its customizability, and its ability to work with oddly shaped products that are more rigid in nature. If you manufacture rigid products or products with odd shapes or sizes, looking into pad printing can potentially save you quite a bit of money via automation and integrating it into your existing production process.