It is a well-known fact that implementing Injection molding robots results in saving on labour expenses, which means that these robots give an excellent return on investment. As contrasting as they may appear, the human arm and the robotic arm are very similar and share common characteristics. They have the same underlying composition of linkages and joints.
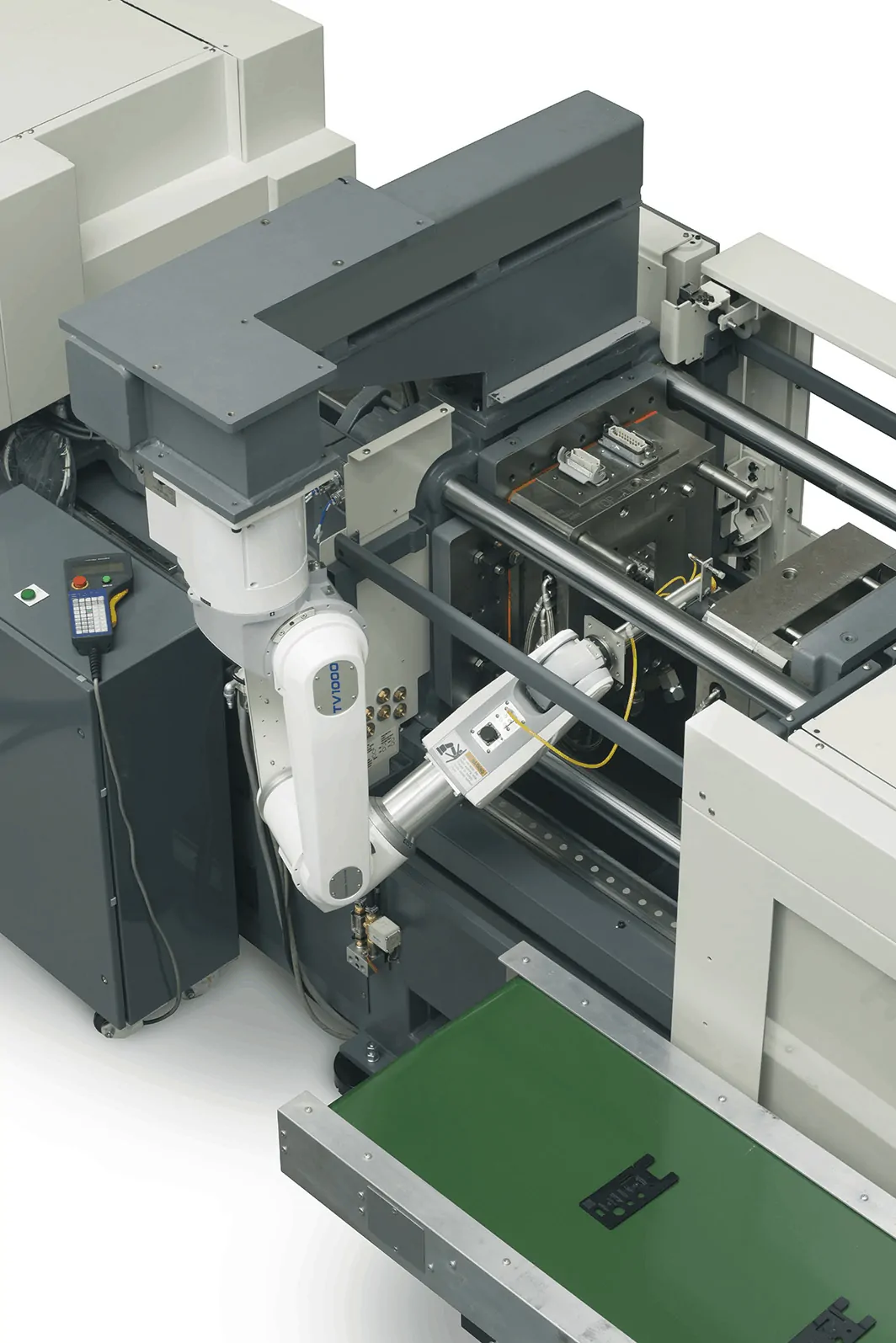
Today’s plastic industry has seen industrial robots used across all areas of plastic fabrication, and related procedures. The similarity to the human arm enables injection molding robots to circumvent any challenge that is presented to them.
It is defined as a manufacturing procedure that produces parts on a large scale.it is a prevalent process in mass production where the same part is produced repeatedly for thousands of times in succession. This procedure has many advantages, and this discussion will divulge into these benefits in detail.
Benefits of Injection Molding Robots
Increased Throughput
You cannot question the increase in throughput when injection molding robots come into play. One of the critical aspects at this point is the robot’s increased production speeds. Injection molding robots work faster in comparison to manual operators, and this surges the number of parts produced per cycle.
Injection molding robots work day and night without tiring, and all that is needed is programming for them to continue producing parts until they are commanded to stop. Thus, it is a no-brainer that increased throughput translates to increased profits.
Shortens Injection Cycle Time
When this procedure is automated, a computer numerical control (CNC) machine and the robotic arms work together. Heating, casting, and cooling processes are carefully calculated without estimations, as would be the case with manual operators.
This reduces the cycle time for every batch of parts produced and it increases efficiency. Also, a robotic arm does not have to wait for an already completed batch to cool down this saves on the time between production cycles.
Increase in Precision & Reduction in Waste
In any injection molding cycle, depending on the level of precision employed, there is some excess material or scrap that remains. The scrap is recyclable, but this requires a distinct procedure where the refuse is removed, and it would slow down the molding process, thus reducing efficiency.
The solution is the automation of the procedure, which makes it perform at a different level of precision, meaning any extra scraps are very minimal. Waste reduction also helps to cut costs.
Improved Quality of Products
It is not prone to errors like manual operators are. The only way errors come into this procedure is if operators feed the wrong instructions to the machine.
A well-programmed robot cannot make errors, and this means each production run is similar to the next. This translates to quality not being diminished as the robot is operating at a high precision level guaranteeing high-quality products.
Repetitive Nature of the Procedure
The process of injection molding is highly repeatable when automated. This means that every fabricated part is similar to the next. Manufacturers must achieve brand consistency, and this helps them to do just that.
Repetition means a master copy can be replicated multiple times, and this will save on production cycle times and hence increase the profitability of the company.
Secondary Processes Efficiency & Effectiveness Role
Secondary processes will increase efficiency and effectiveness only when the procedure undergoes automation. These procedures include pick and place, inspection, and packaging.
This enables the whole procedure to become efficient, leading to more production, increased sales, and increased profit margins.
Conclusion
To sum it all up, first of all, injection molding robots are very crucial in a manufacturing setting. The benefits of these machines are vivid enough, as we have discussed above. The key to most of these benefits being realized, is the automation of all procedures relating to injection molding robots.