The significance of user experience in product design cannot be emphasised. Screw air compressors not only enhance efficiency and performance but also provide a smooth and intuitive user experience. Every component of it, from the interface to the general layout, must be optimised to match the demands and preferences of the operator.
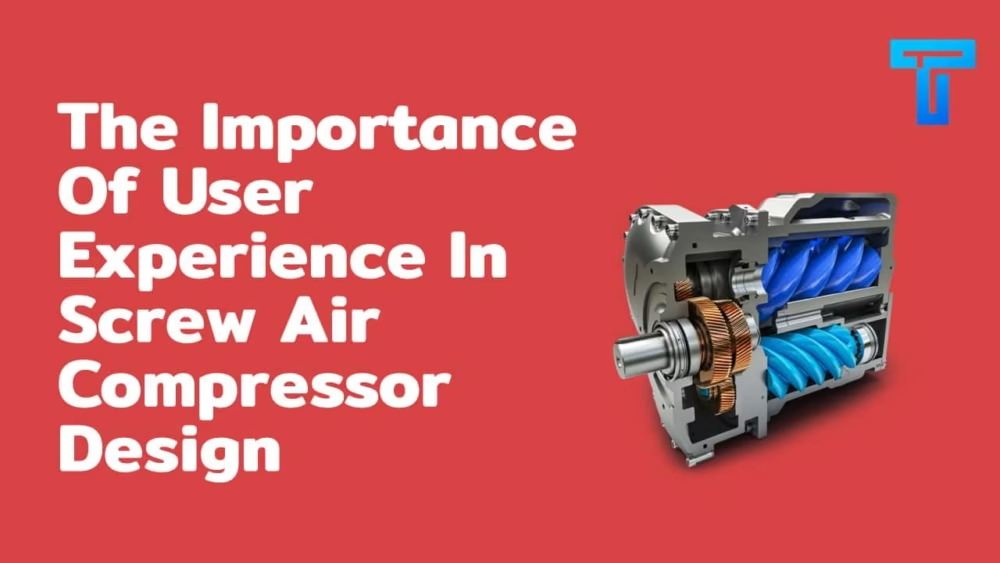
The Importance Of User Experience
Efficiency
Poorly designed compressors can be difficult to operate, resulting in mistakes and inefficiency. If the controls, for example, are not intuitive or straightforward to use, the operator may make mistakes or take longer to fulfil chores. Similarly, if it requires regular maintenance or repairs due to a lack of understanding, it might cause downtime and lost production.
In contrast, a well-built compressor will be intuitive and straightforward to operate, allowing the operator to work more effectively. Clear and straightforward controls, as well as easy access to maintenance areas, may considerably boost efficiency. This can lead to significant cost and manpower savings for the user.
Safety
When utilising a compressor, an operator may mistakenly activate the improper functions or settings if the controls are difficult to operate or ambiguous, resulting in accidents and injuries.
Furthermore, if they are poorly constructed, they may lack critical safety features such as emergency shut-off switches or automatic pressure relief valves. Such features are meant to prevent potentially hazardous situations.
These functions are critical for ensuring safe operation since they can prevent potentially hazardous situations as well as other problems.
Customer Experience
When a buyer buys a product, they want it to meet their needs and perform as described. If a compressor is difficult to use, unreliable, or fails to satisfy the client’s expectations, the customer will be unsatisfied and may not buy the product again in the future.
A satisfied customer is more likely to return to the product and suggest it to others. This can lead to repeat business and favourable word-of-mouth, which can help the company grow and profit.
Aside from repeat business and word-of-mouth advertising, pleased customers are more likely to give good product evaluations and ratings. These ratings and assessments can help a business gain new consumers and improve its reputation.
Today’s shoppers rely heavily on ratings and reviews when making purchase decisions, so good feedback may be a valuable asset for a company.
Best Practices for Screw Air Compressor Design Selection
The Application Requirements
The size, type, and capacity of the compressor required to meet the application’s demands will be determined by the application’s requirements. When deciding the requirements for an application, the flow rate, pressure, temperature, and duty cycle are the most important aspects to consider.
Selecting The Right Type
Screw air compressors are classified into two types: oil-free and oil-injected. Oil-free is appropriate for applications where oil contamination is a problem, such as food & beverage, pharmaceutical, and electronics.
These are utilised when compressed air comes into touch with the finished product and are designed to work without oil lubrication. Oil-injected compression, on the other hand, uses oil for lubrication and unwinding during compression. This aids in the formation of a seal and the reduction of noise levels.
Calculate The Total Cost Of Ownership
A compressor’s total cost of ownership (TCO) includes the purchase price, installation fees, energy consumption, and maintenance expenses during the product’s lifespan. The original purchase price is simply one component of the total cost of ownership.
Furthermore, installation expenses can quickly build up, especially if specialised equipment or services are required. As a result, it is essential to consider installation expenses to ensure that you stay within your budget and that it is properly installed.
Choosing A Reputable Manufacturer
A reputable company’s products are constructed to last and perform dependably because they employ only the best materials and parts. They should also have strict quality control methods in place to guarantee that each compressor is thoroughly tested and fulfils stringent performance standards.
A respectable manufacturer will have a staff of competent engineers and technicians that can provide assistance and support throughout the decision process and the life of the compressor. This may involve support with installation, maintenance, and repair, as well as optimisation and troubleshooting.
Conclusion
A well-built compressor not only enhances the efficiency and performance of the equipment but also provides the user with a smooth and intuitive experience. When selecting or designing a screw air compressor, manufacturers should pay great attention to the user experience. This will allow the company to get more experience in the field.